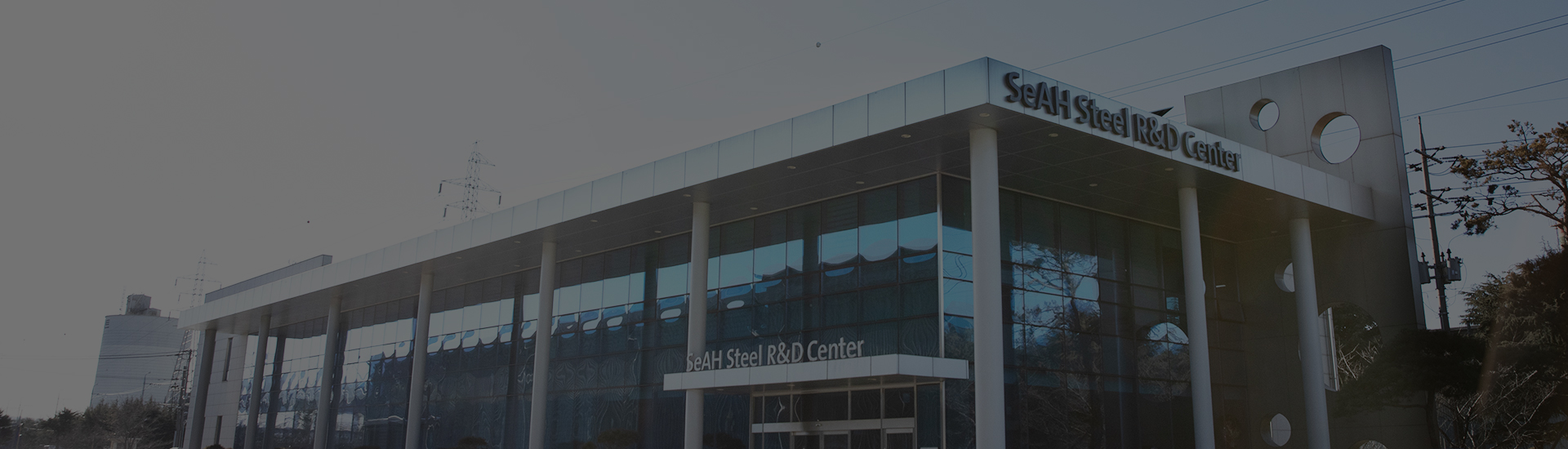
R&D
SeAH Steel's R&D Center is the best research center in Korea's steel pipe companies for discovering new products, technologies, and businesses that drive future growth.
Research Objectives
Securing the future of SeAH Steel through pilot research and development
[Empowerment and Support to Build a Self-Sustaining System]

Field of Research
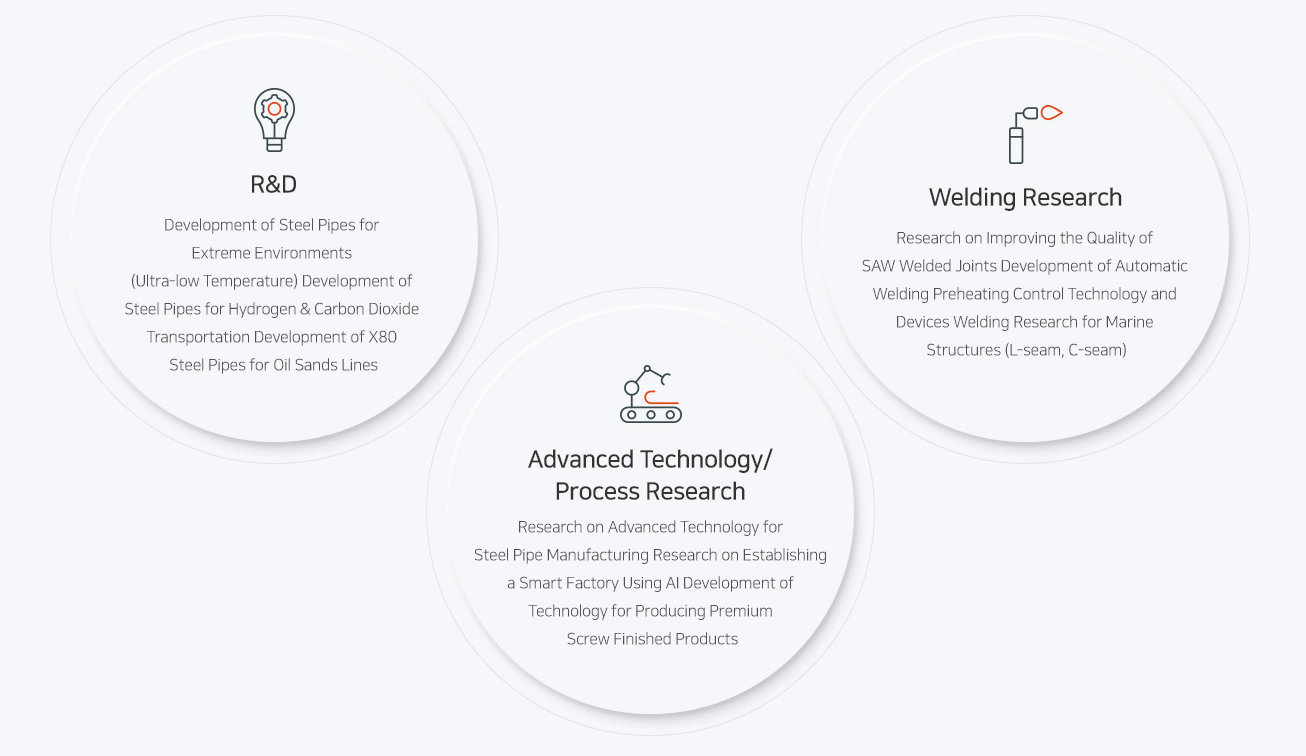
Research and development history
-
- 2022
- 12 Development of X80 steel pipe for SAGD Steam-lines
- 07 Established welding research building
- Built L-Seam / C-Seam / ESW simulator
- 03 Developed STS-Clad steel pipe manufacturing technology
- 01 Participated in two government projects (Development of Core Technologies for Renewable Energy)
- Development of materials and manufacturing technology for high-pressure hydrogen transportation pipes at 100 atmospheres (Apr 2022 - Dec 2025)
- 2021
- 04 Participated in two government projects (Materials and Components Technology Development)
- Developed cryogenic HIC SSCC with -45℃ guaranteed ERW steel pipe manufacturing technology with excellent corrosion resistance properties (April 2022 - December 2025)
- Developed technology to manufacture 16-inch and larger diameter steel pipes for offshore plants and renewable energy for the highly functional energy industry (April 2022 - December 2025)
- 2020
- 07 Constructed new R&D center
- 04 Participated in two government projects (Materials and Components Technology Development)
- Development of steel pipe and pressure vessel manufacturing technology using wide plate rolled clad steel (Apr 2020 - Dec 2022)
- Development of 550MPa riser steel pipe manufacturing technology for shipbuilding and offshore plants (Apr 2020 - Dec 2022)
- 01 Reorganized into R&D Center (Pilot Research Team, Smart Technology Team, Quality Management Team)
- 2019
- 11 SeAH steel was registered as a World Class Product (API K55 and five (5) other items)
- 03 The Pilot Research Team was reorganized into New Technology/Process Development and New Material/Welding Research Part.
- 2017
- 07 Signed a technology agreement with the Pohang Metal Materials Industrial Promotion Agency (POMIA)
- 2015
- 08 Developed steel pipe manufacturing technology using high manganese steel for wear resistance
- 2014
- 06 Participated in one government project (Core Technology Development for Industrial Materials)
- Developed ERW steel pipe technology for mining applications with a yield strength of 110 ksi (758 MPa) or higher (Jun 2014 - Nov 2017)
- 2013
- 06 Participated in one government project (Development of Fundamental Technology for Industrial Materials)
- Development of manufacturing technology for high-manganese steel pipes and components for LNG applications (Jun 2013 - Dec 2016)
- 2012
- 11 Developed element technology for manufacturing High Collapse Performance steel pipes (industry-academia collaborative research)
- 2011
- 12 signed a research agreement to develop steel pipe materials and pipe-making technology for energy transportation (POSCO Technology Research Institute)
- 06Participated in developing steel pipe technology for SOUR within the Ministry of Trade, Industry and Energy's medium-term base project (June 2011 - May 2016)
- 2008
- 06 Researched ERW welding characteristics of alloy steel pipe (industry-academia collaborative research)
- 2007
- 07 Developed quality assurance technology for welded parts of material pipes for a technical support business specializing in component materials (July 2007 - June 2008)
- 2006
- 11 Participated in the development of steel pipe technology for Lifeline within the Ministry of Trade, Industry and Energy's medium-term base project (June 2011 - April 2012)
- 07 Reorganized into new material research, product development, welding technology, and facility technology Parts
- 2005
- 01 The Research and Development Team (R&D Team) reorganized into the Technical Service team (The Facility Planning team was affiliated with the Pohang plant)
- 2003
- 04 Reorganized into R&D team (steel structure research), Facility Planning team, and Technical Services team (3 teams)
-
- 1998
- 03 it was reorganized into two teams: the R&D team and the Facilities Planning team.
- 1996
- 01 Changed name to "SeAH Steel Technology Institute"
- 1995
- 03 operated the task-based responsibility system and organized additional technical support teams (5 teams)
- 1994
- 01 Merged Facility Planning team and Design team. Created additional international TFT teams
- 1992
- 12 Started development of automatic welding heat input control device for steel pipes (industrial-based technology, industry-academia collaborative research)
- 1991
- 10 Reorganized into five teams (Research Management, New Product Development, Facility Planning, Automation Technology, and Design)
-
- 1987
- 05 Designated as a Special Military Service Institute
- 01 Established Technology Research Center (Ministry of Science and ICT Office 411)
- 1977
- 05 Launched R&D department (location: Gaebong-dong, Seoul)
Research and Development Performance
-
1) Development of API X80 steel pipes for Oil Sand SAGD Steamlines
1) Development of API 5CT K55 steel pipe
2) Commercialization of non-heat treated SeAH 80/90 and development of SeAH 100
3) Development of API 5CT QT heat treated steel pipe (L80, N80, P110)
4) API 5CT High Collapse guaranteed steel pipe
5) Green Tube for API 5CT P110 Q/T
6) Development of API 5L X100 steel pipe
7) API 5L Gr.X60, X65, X70 steel pipe for enduring SSCC
8) API 5L Gr.X65, X70 steel pipe for enduring HIC
9) Low temperature (-45℃) steel pipe (for export to the US)
10) Developing ERW 8" thick wall steel pipe
11) Thick wall steel pipe SeAHYPER
12) WRP210 (abrasion-resistant steel pipe)
13) Steel pipe for tunnel reinforcement (N-80, S45C, STKM16A)
14) For hydroforming P.O. Steel Pipe
15) Picking Pipe for chemical piping (for export to the US)
16) Cr-Mo alloy carbon steel pipe for corrosion resistance and boiler tubing
17) Sea water resistant Strong Marine 400
18) Sulfuric acid corrosion-resistant steel pipe
19) Lean Duplex for STS316L replacement
20) Steel Pipe-STRUT (jointly developed by POSCO and 7 steel pipe companies)
21) Marine Pipe (white pipe for seawater piping)
22) Government project development of steel pipe and pressure vessel manufacturing technology using a wide rolled clad thick plate (2020 – 2022) Developed manufacturing technology for 550 MPa riser steel pipes for shipbuilding offshore plants (2020 – 2022) Developed ERW steel pipe technology for mining with yield strengths greater than 110 ksi (758 MPa) (2014 – 2018) Developed technology to manufacture high manganese steel piping materials and components for LNG (2013 – 2016) Developed X80 grade steel pipe for H2S-containing oil/gas transportation (2011 – 2017) Developed technology for manufacturing and application of Hyper Duplex stainless steel for cooling seawater facilities ('08-'14) Developed technology for manufacturing fine-grained steel pipes for future urban harmonized Lifelines (2006 – 2012)
23) Industry-academia collaborative research development of element technology for manufacturing High Collapse Performance steel pipe formation and stress analysis of roll-formed steel pipe by finite element method, alloy steel pipe welding technology, and basic research on laser welding of high-strength steel pipe
24) Comprehensive technical support project for parts and materials research on technology for quality assurance of ERW welds in material tubes, a key technology for quality assurance of weld SSCC resistant
25) Established a new ERW 4” Tubing line (USA)
26) Launched SeAH Steel Vina 2nd Plant (Vietnam)
27) Build a Spiral API line (USA)
28) Build JCO a 500,000 ton line of heavy steel pipe (UAE)
29) Thicken the ERW 5” mill
30) Establish a new QT heat treatment line
31) Establish a new OCTG 20" screw line (Premium screw product)
32) Newly created JCOE 18M line
33) CFT steel pipe support development (new plant established)
34) Build a new ERW line (Vietnam)
35) Development of a welding spark Detecting device (ERW)
36) Develop a welding standard ROI device
37) Developed and patented a welding Waveform Control device
38) Developed a coil width measurement device
39) Developed a heat treatment Seam Tracking device
41) JCOE 18M Press control system development
42) Developed a JCOE straightness measurement device
43) JCOE robotic marking machine automation
44) Developed small diameter Rotary Floop 3x loading technology
45) Developed a 24" Pipe mill crop-share cutting control system
46) Developed an 8" ERW online inner bead-checking device (8"x 16.5T)
47) Developed technology for device removing oil left inside the pipe during an 80ft-long pipe fabrication
48) Developed a 3D weld flaw detection device
49) STS steel pipe Digital RT technology development
50) Developed non-sprayable coating devices
51) Developed an Auto carriage for C-Seam Weldability evaluation
52) Post-heat treatment of 24" ERW Mill
53) Development of hollow rebar prefabrication technology
54) Development of JCOE welding seam trimming and bead cutting device
55) Establishment of production system for angle pipes for Rail Cars
56) Establishment of production system for hydrogen and CO2 transportation pipelines
57) Establishment of production system for threaded couplings (API and Semi Premium Connector)
58) Automation of JCOE insertion crane operation
59) Automation of JCOE cleaning device
60) Introduction of safety accident prevention system
-
1) Anti-Groove corrosion steel pipe (water pipe welded durable corrosion steel pipe)
2) Pipeline for Sour Gas (API 5L X60)
3) Oxygen-free atmosphere heat-treating facilities
4) Ultrasonic flaw detection technology
5) Large diameter roll bending Mill
6) Operate facility monitoring devices
7) Ministry of Commerce Industry and Energy: Joint research on industrial-based technologies - Development of automatic welding input heat control technology (1st year)
8) New equipment introduced - Ti Tube pipe maker, Full Body UT, etc.
9) Collaborative research - steel pipe corrosion and anticorrosion research, steel pipe pile application development research, low to mid-rise steel-framed apartment research
10) Promote steel pipe technology transfer business overseas (APC-TA)
11) Established a joint venture in Vietnam (Hải Phòng, VINA PIPE)
12) Automate galvanizing pretreatment facility operations
13) Equipment live monitoring devices
14) Established new ERW 24" Mill (Unit PM53)
15) Established a joint venture in Vietnam (Ho Chi Minh City, SPC)
16) Automate galvanizing pretreatment facility operations
17) Equipment real-time monitoring devices
18) G7 Task: Collaborate on the development of superconducting CICs (discontinued)
19) Automotive pultruded header piping (for shock absorber, Axle, Stabilizer, Drive Shaft)
20) Steel pipes for hydraulic cylinders
21) Seismic angular & architectural steel pipe BCR295, KS D 3864, STAS 490, STKN 490
22) High-tensile steel pipe for pylons (STKT 590)
23) Steel pipe for Slurry
-
1) Developed electric pole
2) Commercialization of insulated double pipe development
3) Development of ASTM A178 Gr.A for boilers
4) API 5CT N-80 steel pipe development
5) API 5L X52 HIC-Free
6) Installed 3-Roll Bender Mill (LD80)